
Chapter 1
A race against… what?
Sustainability and resilience continue to dominate the manufacturing industry.
The growing pressure from customers to produce sustainably requires manufacturers to rethink their operations. A recent study of IPCC highlighted that manufacturers account for 30% of global greenhouse gas emissions, being manufacturers’ biggest environmental priority alongside waste reduction.
EY Future Consumer Index
38%of global consumers believe businesses should prioritize responsible production and consumption of goods and services. (EY Future Consumer Index)
Leading manufacturers recognize the need for action in this area, particularly within the context of COP26, where the importance to reduce and avoid emissions has been emphasized again. A recognition translated into initiatives to decarbonize their operations, requiring an “over the wall” approach with strategic partnerships across your supply chain for business partners to demonstrate a commitment to decarbonization as well.
There isn’t one definition of ‘leading practice’ – however, sustainability practices are paramount for most manufacturers today.
Sustainability can mean different things to different people. Knowing how important it is for customers to know they’re buying from an ethical business, manufacturers are continually looking for new ways to innovate in that space. We are seeing all COOs building their own “Save the Planet” strategy to deliver a better future through the goods they make. A proactive strategy meaning different things for different people, setting sustainability at the heart of everything they do. From where they source their raw materials and energy to power factories, right through to their packaging and how they dispose of production surplus. Innovation with people at the core – driven by profitable growth, accelerated by technology.

Chapter 2
Paving the way forward!
An acceleration of diverse sustainable manufacturing practices makes it difficult to focus efforts.
Four areas of impact
Sustainable manufacturing begins with the value chain. But what does it take to reframe the future of your “Green Factory”? There are four main areas of impact to prioritize for measurable results of sustainable practices.
1. Product Design
Up to 80% of a product’s lifetime emissions are determined by decisions made at the product design stage. By building on proven cost-optimization techniques and including greenhouse gas emissions in the simulation and trade-offs you make, you can get those choices right. Furthermore, labor and energy costs have risen, as have the costs of raw materials. A greater focus on MRO and alternative sustainable materials are key in achieving goals.
How EY can help? Supply Chain Transformation.
2. Operational Excellence
Investments in operational excellence programs to improve operational efficiency and reduce waste have been a focus area for decades. However, organizations are struggling to reach breakthrough or sustainable results. Our successful EY and P&G alliance to achieve operational excellence in manufacturing is now used in +400 smart factories resulting in savings of ~$15b.
How EY can help? EY and P&G Alliance.
3. Lifecycle Packaging
Flexible, green or eco-friendly packaging have shifted from ‘buzz’ to ‘normal’. Accelerated by the pandemic and ever-increasing regulations, both the need to reinvent ways of working and the rise in public awareness have led manufacturers to swift action and bold commitments. Continuous developments and leading trends are driven by breakthrough innovative concepts – from biodegradable or compostable to bioplastics. However, the ever-popular reduce-reuse-recycle is here to stay.
How EY can help? Climate Change and Sustainability Services.
4. Carbon Footprint
Getting to net-zero and circular are the next big opportunities for manufacturers, as explained in our latest EY podcast on The Future of Supply Chain. Using innovative and sustainable solutions like renewable electricity resources or green hydrogen will be the next normal to run factories. Energy management should be seen as an important part of any decarbonization journey. Good energy management performance is not just a legal obligation or proactive commitment but it also makes good business sense to create long-term value. Complementing with and accelerated by smart factory platforms help achieve breakthrough results on the bottom line.
How EY can help? EY Smart Factory.
Operational excellence and Industry 4.0 walk into a factory… Actually not a joke, but a synergy to unlock both sustainable growth and environmental sustainability.
Three key pillars: people, technology and processes
Focusing your efforts on reframing the future doesn’t eliminate the need to think about the foundations to support this transformation. There are three key interdependent pillars of your organization that should work together: people, technology and processes.
- Put people at the center of your transformation. Besides leadership commitment, you need to win the hearts and minds of your entire workforce and communicate in such a way that your strategy speaks to all levels of your organization. Only then sustainable manufacturing can be achieved. Furthermore, this helps to unlock the full potential of the technology being deployed. For many COOs, the answer is upskilling or retraining of the existing workforce. In the near future, even now, your team needs to be managing trainers, curricula, and skills-building to elevate the workforce of tomorrow.
- Greenwash technology. Sustainable operations cannot be decoupled from technology. The one is the opportunity of the other; and budgetary constraints for sustainability initiatives could even be resolved by routing the benefits realized from investments in smart technologies into sustainability programs. Emerging technologies have enabled businesses of all sizes to reduce waste, increase efficiency, and gain visibility across the entire value chain.
- Implement processes in a structured and consistent manner to ensure an optimal balance between environmental and economic sustainability. Incorporating sustainable ways of working are critical aspects of any sustainability initiative.

Chapter 3
Time for action
Growth is a foundational enabler of progress toward sustainable operations, a funding catalyst for the transformation imperative.
As highlighted above, sustainable practices are no longer just a compliance exercise but a new source of competitive advantage. Tackling the four priorities are truly transformational, but a key ingredient for success is building a transformation journey to drive material and immediate benefits quickly.
But before starting development, have you valued what it means to be sustainable? Answering this critical exam question requires a hands-on approach to safeguard a successful journey.
1. Align value chain and organization’s vision
First, align the sustainability agenda and your organization’s sustainability goals with your value chain strategy. A current and future state assessment will help you identify where your value chain can add maximum value and prioritize initiatives accordingly.
2. Create an action plan and roadmap
Having aligned on objectives, develop your business case and gain stakeholder alignment to drive maximum value and buy-in across your organization. Consider what technology solutions could enable your transformation. The transformation roadmap translates your prioritization into a combination of quick wins and long-term benefits.
3. Activate and execute strategy
You are now in the starting blocks to execute your strategy, delivering ROI quickly while creating long-term value by activating your roadmap. This may include appointing new roles and responsibilities to lead the initiatives at the strategic level. Appointed leadership will assess and evaluate the impact throughout the journey and take forward the lessons learned as you continue rolling out your strategy to continuously improve.
How EY can help? EY CogniStreamer.
Making real difference doesn’t require a big bang. It requires a cultural focus on small wins with big impact - a culture embedded across your entire value chain.
Impact at scale
Only very few sustainable initiatives that are launched are actively being scaled across organizations. Selecting your priority areas will help you to create impact at scale – guided by a culture of “lifecycle thinking” through the right people and knowledge, enabled by the right technologies, and supported by the right processes to optimize the lifecycle of your manufacturing systems, products and services. To make a real impact, COOs should select profitable practices. It’s profitable if it’s scalable. And if it’s scalable, the impact can be extremely powerful. Impact at scale can only be achieved with the right people, with the right expertise, and the right incentive.
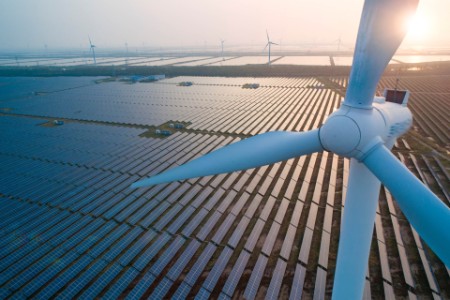
Chapter 4
Green Factories in action
How to realize the value in practice.
The majority of consumers are prepared to pay more for products produced in a sustainable way (EY Future Consumer Index). They now expect transparency in operations and leading organizations are offering this risk alienating risk – balancing risk management and risk mitigation to create competitive advantage. In the last few months, the industry has continued to invest in redesigning packaging responsibly, redesigning products, reducing energy consumption, recovering and recycling water usage during manufacturing and carbon-neutral factories.
As you move up the net-zero ladder, irrespective of your maturity and complexity, you need to understand your business’ energy use. To illustrate this, let’s deep dive into the hot topics of these two key focus areas for nearly every COO: Energy Management and Hydrogen.
Smart Energy Management. Knowledge is power
Energy consumption is generally well understood at a high level, but manufacturers need to more clearly understand its origin, destination, distribution, and potential to reuse. There is a renewed focus on energy management and when it comes to smart factories, it’s time to get out of pilot mode and deliver real change at scale in this area. Smart Energy Management solutions treat energy, air, and waste as a part of the production bill of materials and respond to energy waste in real-time. This helps to optimize energy use, reduce costs (especially valuable in times of increasing rates), harness new revenue streams (reducing payback time of investments), improves operational resilience (by cutting unplanned downtime of critical assets caused by energy power outages) and helps to reach decarbonization goals.
As a critical first step towards energy management, start by mapping out the current state of energy consumption and establish a baseline (at category or regional level) from which to improve performance. Next, define your vision and mission and set targets. To support decisions about the future roadmap, perform a cost-benefit analysis and develop a business case that includes incentives and opportunities.
Green Hydrogen. From net-zero to net-positive
The importance of hydrogen in the transition to decarbonization is no longer in doubt. Its ability to store large amounts of energy over long periods of time at competitive costs (compared with current battery technology) provides a cost-effective solution to seasonal imbalances between renewable generation and energy consumption. Despite remaining challenges to achieve its full potential, new technology, the right incentives and accelerated reduction of energy bills up to ~45% help to unlock profit in EBITDA and top-line growth.
As technology advances and costs come down, green hydrogen has an enormous potential to play a huge role in reaching your net-zero goals. Leading manufacturers have therefore created an ‘hydrogen ecosystem’ with its stakeholders, and its investors in particular. Their combined efforts to research, develop, and produce the technologies needed will be instrumental in reducing the cost and increasing the efficiency of hydrogen applications.
As a COO, you should monitor this market closely. Continuous regulatory developments and technological advances could quickly lead to opportunities to seize a competitive advantage. This is an important reason to consider green hydrogen now versus five to ten years from now. Bringing several opportunities for investments in this unlimited resource, we advise to start with a pilot implementation before scaling up. Start with a feasibility study to work out the future set-up with a concrete business case and value proposition. This may include scenario modeling for a partner ecosystem and planning for the pilot project.
Newsletters EY Belgium
Subscribe to one of our newsletters and stay up to date of our latest news, insights, events or more.
Summary
What started as a compliance exercise has become a strategic business imperative. Sustainable operations is the new source of competitive advantage and the biggest driver of transformation. COOs who stand still will fall behind in the race for market-leading growth. As a strategically leading COO you should guide – just as your CEO – your business toward a successful rebound, not back in time, but fast forward to a future of more sustainable and purpose-driven growth. If you aren’t already thinking about how your manufacturing value chain creates long-term human, social, economic and environmental value, now is the time.